Manufacturing Facilities
How We Manufacture
Our Products
Phase 1
Raw Material Extraction
Transportation of extracted raw material: The extracted raw materials are loaded by loaders onto trucks and transported to either a buffer stock and/or directly to the crushing plant.
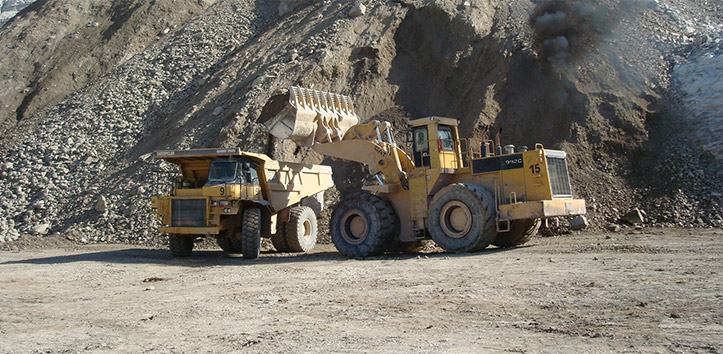
Phase 2
Raw Material Crushing
Phase 3
Raw material storage and pre-homogenization
Preparing the raw mix stock: The crushed raw materials are blended, analyzed and then transported via belt conveyors to the stacker that travels up and down alongside the storage area for buildup pre-homogenization longitudinal raw mix stockpile using the "Chevron method" of stacking.
Raw material transport to grinding plant: A reclaimer rakes down the raw material from one end of the pile so that material is reclaimed from its entire section. As a result, the re-claimed material contains material from all pile layers i.e. variations in chemical composition are negligible. The reclaimed material is transported via a long belt conveyor to the grinding plants.
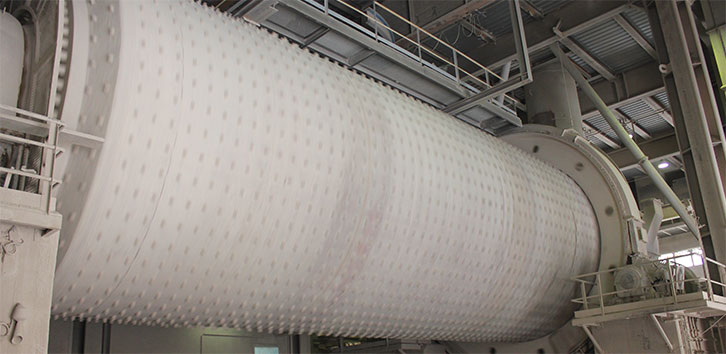
Phase 4
Raw material drying-grinding
Raw materials are fed into a ball mill which is basically a large "tube" with balls of varying sizes inside. When it rotates around its longitudinal axis, the balls are thrown about inside the tube. As a result, the raw materials are ground to a fine raw meal. The raw materials are also dried in the mill by means of hot gas from kilns and/or from a hot gas generator. The finished dried and ground product is called "raw meal." The fineness of the raw meal is controlled by the CN laboratory.
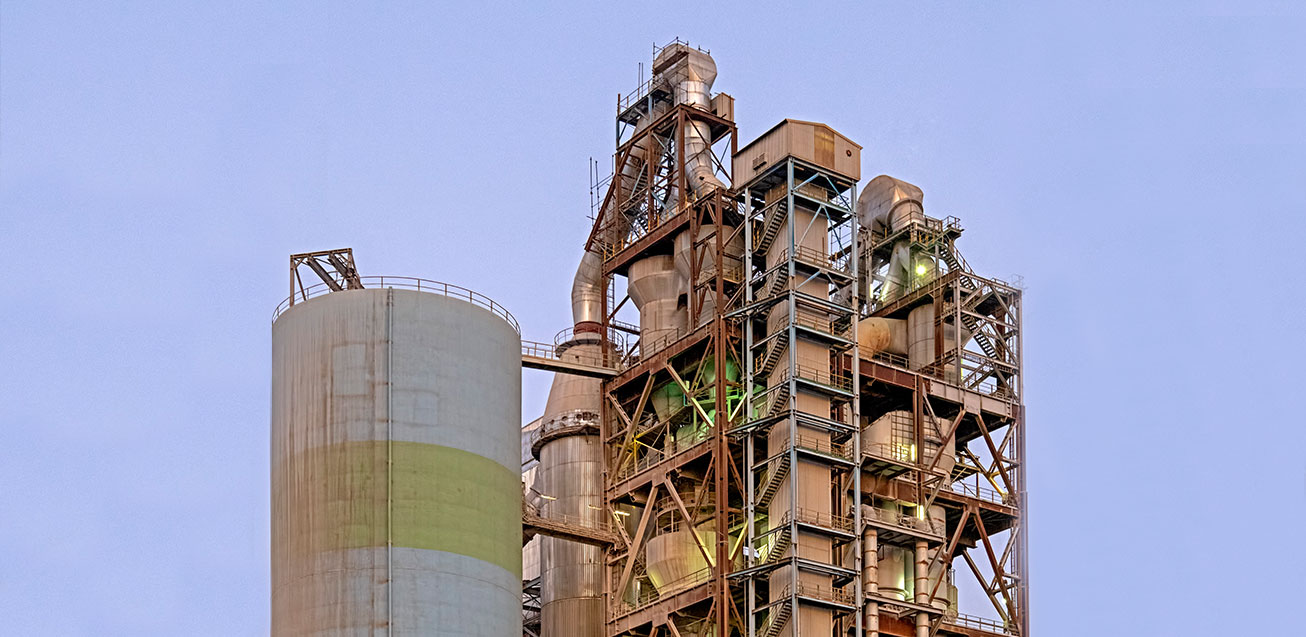
Phase 5
Raw meal Homogenization and Storage
Phase 6
Burning process
The raw meal is transformed into clinker (semi-finished product) by heating it to a temperature of about 1450 °C in rotary kilns. Rotary kilns are tubular, with a diameter of three to five meters and a slope of more than 3% to help material flow. The hot finish - burnt clinker falls down from the kiln into a grate cooler where it is cooled by means of cold air passing through the holes of the grates.
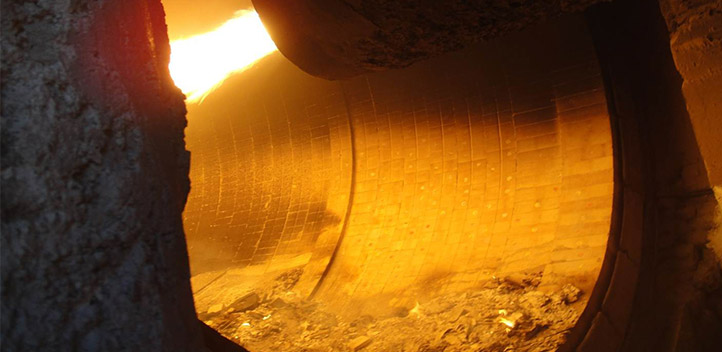
Phase 7
Cement grinding
The Cement (final product) is obtained from grinding a mixture of clinker with gypsum and other additives such as pure limestone, slag, pozzolan, etc.
Grinding is performed in two steps:
1) Pre-grinding of the mix of clinker, gypsum and additives to intermediate small size particles by means of roller press
2) Grinding of the roller press output by means of a ball mill which is basically a large "tube" with balls of varying balls sizes inside. When it rotates around its longitudinal axis, the balls are thrown about inside the tube causing the mix of clinker, gypsum and additives to be ground into fine powder by the impact and attrition of these balls.
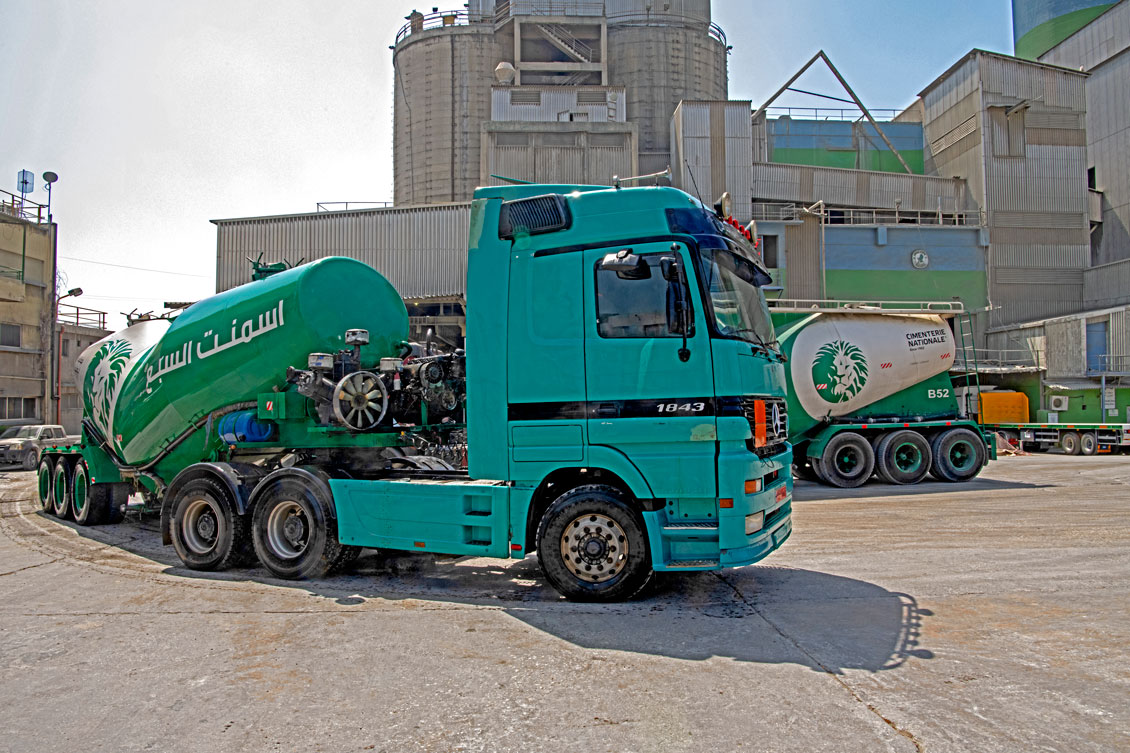
Phase 8
Cement packaging and delivery
The cement is distributed to customers locally and beyond (export) either:
- Packed in Bags of 50kg and transported by means of on high way trucks
- Packed in Jumbo bags (1500kg) and transported by means of on high way trucks or ships
- Packed in Sling bags and transported via ships
- Bulk (by trucks or via ships)